Design, Modeling, Simulation, and Testing of Flexible Joint
Volume 12: Mechanics of Solids, Structures, and Fluids; Micro- and Nano- Systems Engineering and Packaging(2021)
摘要
Abstract Metal materials are used widely in industry for piping, as they provide desirable material properties for use in harsh environments. In this work, we explore different flexible pipe joint designs that enable fluid transport in flexible heat transfer devices. Flexible joints would allow heat transfer devices to fit in variable cooling areas. The proposed flexible joints will be 3D printed in metal with the goal of maximizing their bending angles, while minimizing volume. The objective of this research is to develop flexible pipes to connect parts involving fluid flow, and we propose three types of flexible joint designs: 1) helical coil spring, 2) torsional coil spring, and 3) serpentine structure. Then, we introduce a low-cost design process to improve these joint designs. Metal 3D printing offers increased design flexibility in comparison to traditional metal manufacturing methods. However, metal 3D printing can be labor intensive and costly, thus the number of design iterations using metal printing should be minimized during the design process. To reduce the frequency of metal prototyping, we used plastic 3D prints for rapid prototyping and evaluation. The flexible joint design considered the effects of pipe shape, pipe size, pipe diameter, free length, and total pipe length. Although mathematical models exist for the three types of flexible designs, they tend to be complex, difficult to implement, and specific to certain types of boundary conditions. In our experience, it is faster and more meaningful to perform experimental parametric studies using plastic prints due to accessibility and cost-effectiveness of plastic 3D printers. However, analytical models do offer significant insights during the design process. Thus, we developed simple analytical models for each of the three types of flexible joint designs which can be used in the initial design phase. Tests were performed to characterize the designs. Then, finite element simulations were performed for plastic prints and these simulations were validated against experimental data. We show that the results from analytical models, finite element simulations, and testing results for plastic prints are consistent, and these tools can be used to predict performance. In this paper, we discuss the following findings: 1) development of simple analytical models, including successes, limitations, and challenges; 2) the role of finite element simulations in the design process; 3) testing results from the three types of joint design; 4) quantification, interpretation, and discussion of testing results.
更多查看译文
关键词
flexible joint,helical coil spring,torsional series spring,serpentine structure,angle of deflection,von Mises stress
AI 理解论文
溯源树
样例
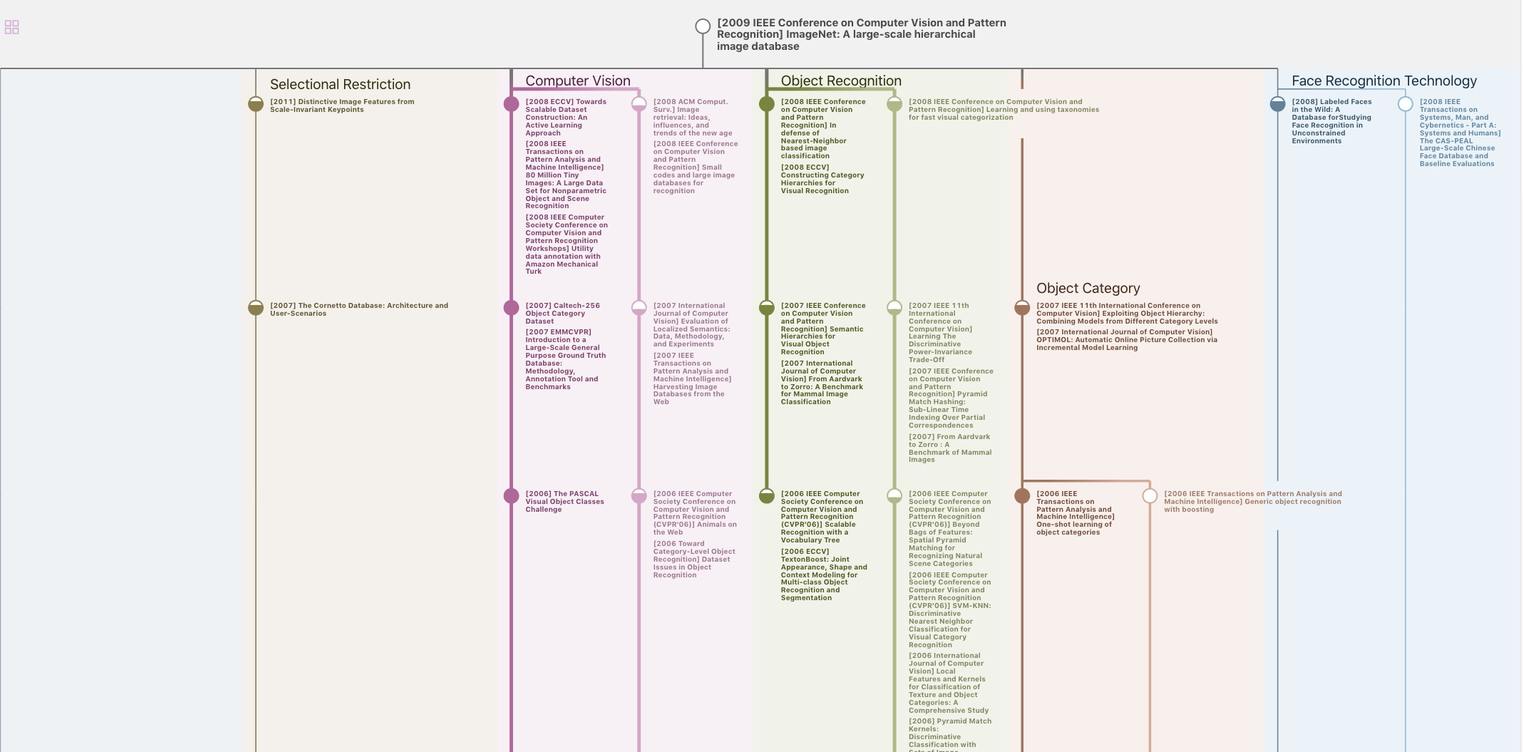
生成溯源树,研究论文发展脉络
Chat Paper
正在生成论文摘要